The cold storage supply chain is a vital component of global fruit and vegetable distribution.
ROTTERDAM, Netherlands — On both U.S. coasts, vessels set sail carrying grain and dry goods across the Atlantic or Pacific. Yet beyond these visible bulk shipments, a sophisticated network of cold storage containers ensures the seamless international trade of fresh fruits and vegetables.
Whether by truck, ship, or plane, the journey from farm to market is a logistical feat, requiring precision and scale.
However, the United States does not engage in global shipping and logistics like much of the world. Not a single U.S. port ranks among the world’s 10 largest — a distinction belonging exclusively to Asia and Europe, according to the World Shipping Council.
While often unnoticed, the cold storage supply chain is essential for keeping international fruits and vegetables moving across global markets.
The Netherlands: A global agri-food hub
One European country dominates global fresh produce trade, responsible for 60 percent of the world’s floriculture exports and 20 percent of fresh produce imports from developing countries. With nearly 8,500 food processing companies reliant on imported raw ingredients, the Netherlands has mastered logistics and supply chain efficiency.
Home to Europe’s largest and most modern port, the Port of Rotterdam, the Netherlands plays a critical role in global food trade. The port is in a strategic location on the Dutch coast making it an ideal logistics hub, benefiting from historic maritime roots, deep foreign trade investments, private tech funding, and a highly efficient agricultural sector.
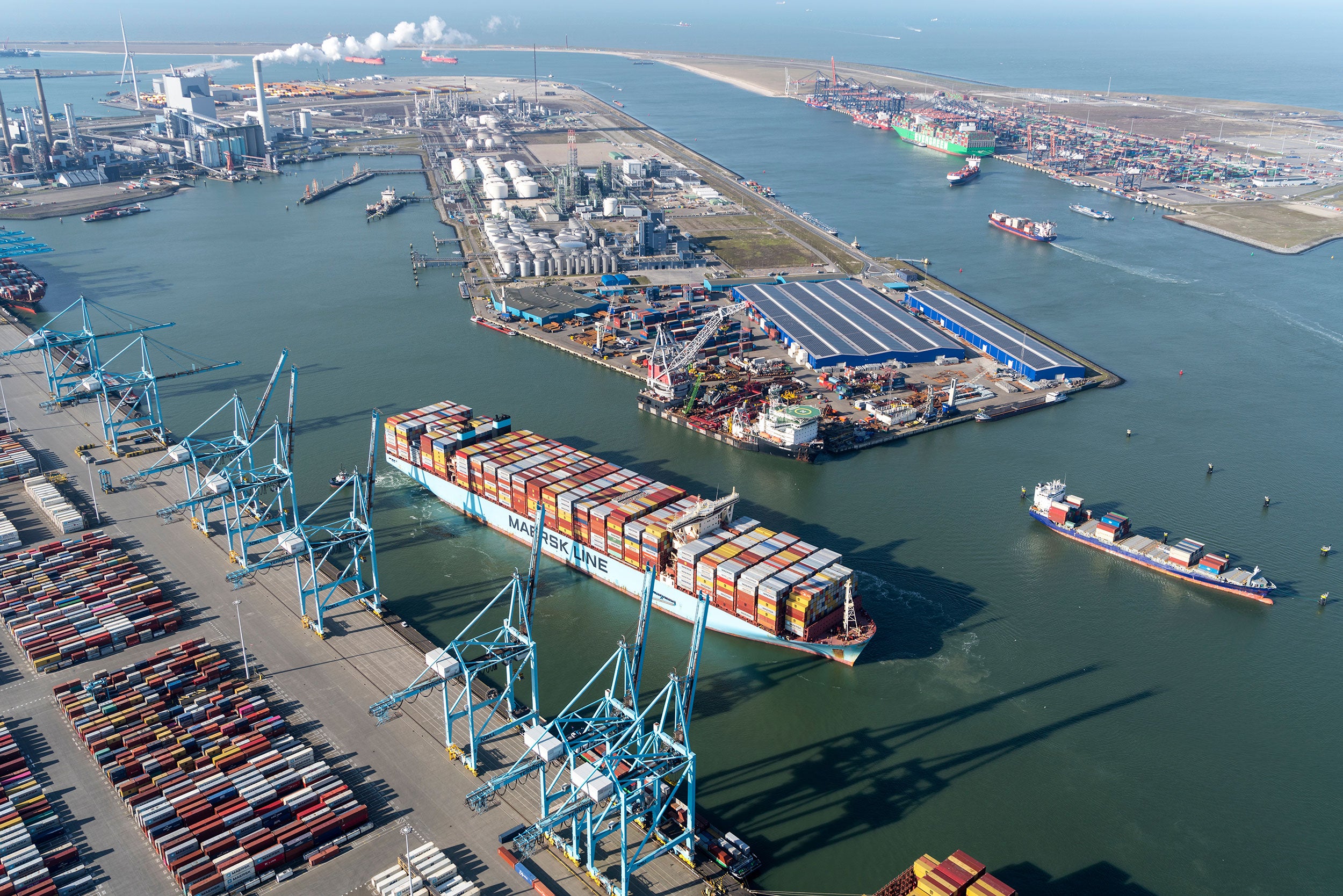
Ultimately, it’s not just the amount of agricultural land used to produce food or the total food production per continent that matters. Rather how each region manages urbanization, farm decline, and feeding a population surrounded by water. For Europe, this relies on trade and imports.
Rotterdam functions as a transshipment hub, specializing in imports and helping to unload cargo for repackaging and redistribution across Europe.
Towering cranes at the Port of Rotterdam, Europe’s largest seaport, unload a Maersk container ship arriving from Singapore after a 38-day journey around the Cape of Africa. Each container — blue, green, or orange — belongs to different shipping companies, while the white refrigerated units, known as reefers, reflect sunlight to maintain optimal temperatures.
Companies such as Hapag-Lloyd, Evergreen, Costco, MSC, Yang Ming, and Maersk are all shipping containers companies, which use the northern port for inbound arrivals.
At the Maasvlakte 2 facility, the newest addition to the port, operations run like clockwork. With a footprint of 20 square kilometers (nearly 8 square miles), the facility welcomes over 50 vessels daily, loading and refueling for their next journeys.
Construction began in 2003 and is set for completion in 2035, expanding the port’s capacity by 20 percent to handle 17 million containers annually. Almost 4 percent of the Netherlands’ gross domestic product (GDP) is tied to this port alone, the Port of Rotterdam notes.
Shipping perishables: A high-stakes game
Perishable goods depend on refrigerated cargo units to keep fresh fruits and vegetables in optimal condition during transport. Though fresh produce makes up only 10 percent of incoming cargo, these refrigerated containers allow produce to stay fresh for weeks or even months.
According to the University of Maine, the approximate storage life for commonly shipped crops is grapes, two to eight weeks; nectarines at two to four weeks; apples up to 12 months; cabbage at five to six months; and sweet potatoes at four to seven months.
The arrangement of containers on each cargo ship is carefully orchestrated — reefer placement is highly strategic, ensuring accessibility for crew members to monitor and service containers mid-voyage.
“There must be enough empty containers sent to key production regions before peak harvests,” explained Bernhard Stade, vice president of the global reefer center at DHL, a production company of cargo containers. “As always, price is dictated by demand in trade and logistics.”
Reefers remain plugged in for most of their journey, except when delivered to the port and during transfer from pre-storage to the pier before loading onto a vessel. Once at sea, reefers are remotely monitored using mobile or returnable tracking devices.
High-value crops, like avocados, mean a high-value operating system in the sector.
“Reefer containers need to be maintained after every trip for cleanliness, steam-clean them, and ensure the cooling system is fully functional for the next trip,” Stade said.
Avocados require a temperature of 40 degrees Fahrenheit with controlled humidity while being transported on a cargo vessel — one of many foreign-grown products experiencing growing demand in Europe.
Kenya is leading avocado exporter to Europe.
“About 70 percent of our avocados go to the Netherlands,” said Alice Okello, the managing export director for KE Limited, based in Kenya. “Eighty percent of the time, we use sea freight; the rest is air freight for premium products.”
The country’s avocado industry has boomed since the 1980s, driven by rising demand and a competitive edge over traditional producers. Kenyan farmers are expanding into new regions to extend the growing season and maximize exports, influenced by European demand.
Once imports from the world arrive in Rotterdam, a company like Maersk oversees value-added services such as re-bagging, sealing, netting, and processing food before it continues along the supply chain.
The inbound produce facility spans 35,000 square meters and is equipped with 16 cold rooms for perishable goods, 62 trucking docks to ensure efficient land-based distribution, and temporary mobile racking and cold storage for inbound shipments.
Produce might stay less than 24 hours in the facility before it is trucked to markets and buyers across Europe.
Standardized containers, pooling systems
One tool that puts Europe at the top of the list of efficiency is Euro pooling containers — the hard plastic containers used to move produce around the continent.
The same green or blue containers, depending on the size of fruit or vegetable, can be found at every stop of the supply chain.
The containers are used by BelOrta, a produce cooperative spanning Belgium and the Netherlands, with 1,000 farmers producing a significant share of the EU’s asparagus and other high-value crops.
Following the principles of the circular economy, they say it has simplified transactions in the sector, especially for farmers. However, “Larger supermarkets are driving the universal pooling and packaging,” said Jo Lambrecht, manager of sales and marketing at the cooperative.
Produce is stored, shipped, and sold in reusable, washable plastic containers, simplifying logistics at every step. BelOrta is one of the many locations that houses, washes these containers.
Unlike cardboard boxes — which can tear, get wet, and are difficult to handle — these containers improve efficiency and reduce waste.
The foundation of efficiency in the EU market starts at farmer-led cooperatives, a stark contrast to the fragmented supply chains elsewhere. In the Netherlands, cooperatives control 83 percent of agricultural output; in Finland, 79 percent; in Italy, 55 percent; and in France, 50 percent, according to the EU Commission.
BelOrta takes part in global trade. Produce is harvested in the afternoon, transported to a massive warehouse, and auctioned off the following morning to buyers worldwide.
Cucumbers, tomatoes, asparagus — whatever is in season for northern Europe — can be found in this warehouse. Within hours, trucks distribute produce across Europe or to ports for global shipment.
This is the third in a four-part series of on-the-ground reporting from Europe, exploring the demands of consumers, the actions of policymakers, and the perspectives of agricultural producers working within the diverse, parliamentary framework of the European Union.
Jake Zajkowski is a freelance agriculture journalist covering farm policy, global food systems and the rural Midwest. Raised on vegetable farms in northern Ohio, he now studies at Cornell University.