Built with 130-150 hp and autonomous capabilities, John Deere’s forthcoming Battery Electric Vehicle lineup is striving to be equivalent to their diesel counterparts
BURREL, California — An EV tractor that is almost identical to how you drive your car?
Representatives from John Deere hosted an exclusive look at their new E-Power tractor prototypes in Burrel to coincide with the World Ag Expo, held February 11 to 13. The event provided producers, dealers, and media personnel with the chance to get a closeup look at Deere’s Battery Electric Vehicles (BEV), anticipating full production in the next couple of years, as a way to meet their 2030 sustainability goals.
The event showcased the first, fully built from the ground up, battery-powered prototypes in three different configurations: an orchard, vineyard, and livestock tractor with a loader. The goal is to have scalability from one machine to the next, autonomous capabilities, intuitiveness, and provide customers with another option to fit their needs and solve problems surrounding labor shortages, environmental concerns, and employee training.
The product development strategy, according to John Deere representatives at the showcase, is to provide customers and dealers the opportunity to test the machines from the beginning and provide valuable insight and feedback in order to ensure the machines are performing to fit industry needs before rolling out to customers.
All machines displayed were similar in both function and base set of features — from the control system in the cabs, vehicle architecture, Gen 5 display, electronic controls for traction system and hydraulics, and steering and braking. They were also all similar to their 5ML series diesel counterparts, including overall lift capacity and max permissible weight.
Each tractor in the lineup featured foot brakes, accelerators, cruise control, and an ultra-quiet ride that the company says translates to better animal husbandry practices, comfort for the operators, and noise reduction for jobs that require close proximity to public spaces such as schools. The power range of the lineup of tractors will be about 130-150 horsepower, equivalent to their diesel counterparts.
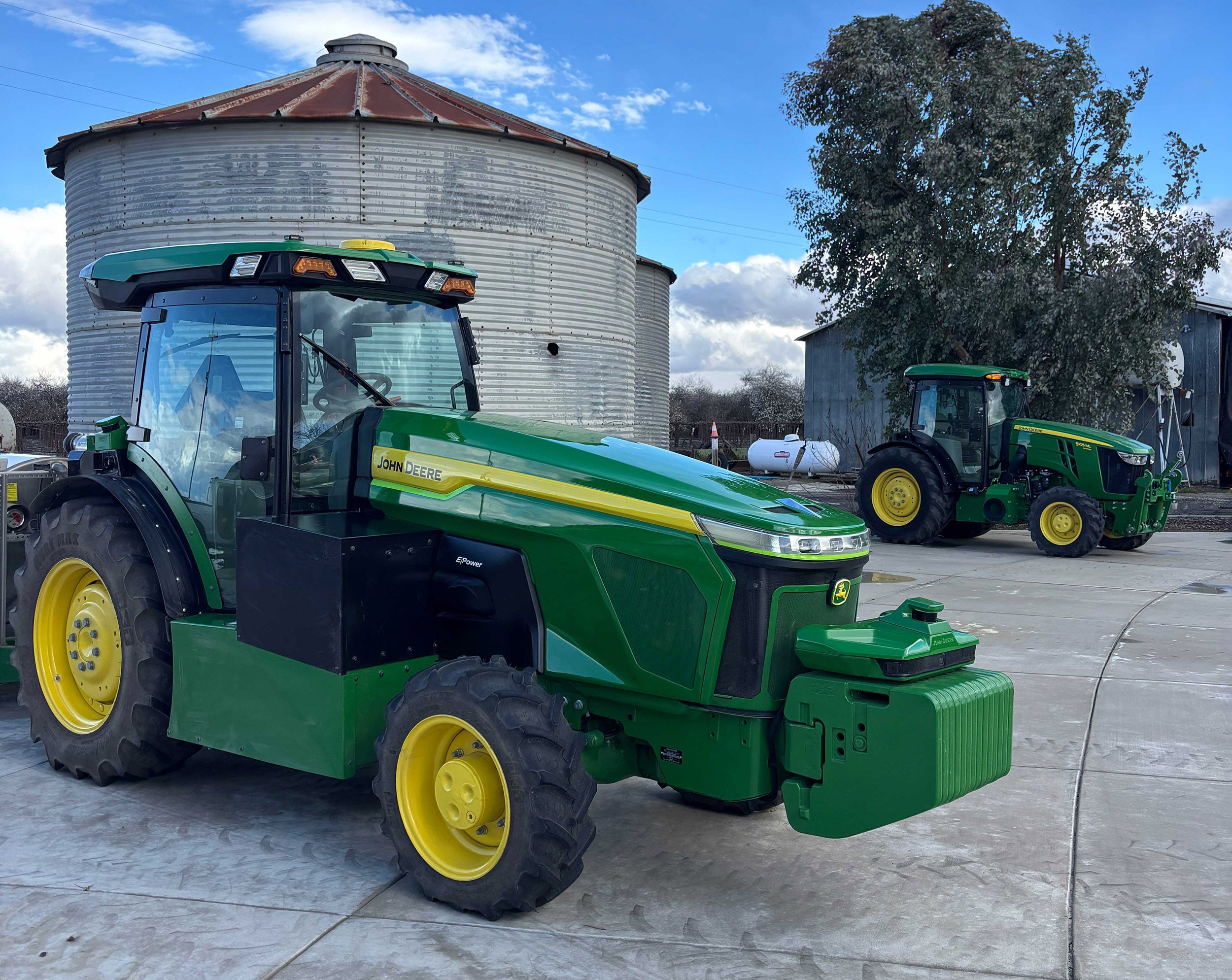
Representatives at the event highlighted the savings benefits of their E-powered machines are less fuel usage and less maintenance, such as a 2,000-hour hydraulic oil change and daily maintenance inspections in the filters and the cab. Additionally, there are no engine oil changes or engine air cleaners, and these machines have fewer parts than their diesel counterparts.
In front of the cab, on the left-hand side of each machine, is a common electrical charging port. The highlight of this port is that customers can easily access charging cables that are already on the market, and even purchase from common online retailers if they choose.
The charging provides power to the numerous batteries within each machine. For example, on the vineyard machine, there are five batteries: one on the base of the chassis, three under the hood, and one on the right-hand side of the engine. The energy is distributed through many individual circuits that control the tires, hydraulics and a number of different functions so when the tractor is on, but nothing is being used, all of the distributed motors are shut down allowing for precise control.
The tractors were designed in this manner to lend themselves to modularity and sizing the machines for exactly what the customer needs in terms of power. If a customer doesn’t need all five batteries, they can size down the tractor to fit their operation’s desires.
There is also no need for electric implements, as the back of their BEV tractor lineup features the same design to fit common hydraulics, PTO, and three point, and fits traditional sprayers and other equipment without transitioning to a full new implement lineup as well.
The batteries are designed with active thermal management system by Kreisel Electric, which John Deere acquired majority ownership over in 2021. All of the cells inside the battery packs are designed with liquid immersion cooling that allows Deere to widen the operating temperature so that customers are able to run their machines in extreme outdoor temperatures safely by keeping the cells at a consistent temperature.
Keeping batteries at neutral temperature provides longevity and slower degradation while decreasing recharging time.
Charging time depends on the on the size of the charger, and while the prototypes are at about an hour re-charging time, John Deere is working on decreasing this time substantially so as to fully re-charge within a work day’s lunch break. And rather than dealing with swapping batteries, their goal is to find ways to quick-charge and prevent downtime.
The intent for battery lifetime is to be the same as the life of the vehicle and upgrade batteries if new technology is created. With the John Deere Operations Center, and multiple sensors, the health data of the machine will be communicated remotely to the owner/operator and provide real-time information to monitor systems.
The Operations Center is John Deere’s digital farming platform, which customers use to monitor the progress and activities that are occurring on their operations, while ensuring their battery charges will either last for the entire task at hand, or re-charge quickly enough to return back to the task as quickly as possible. They can also analyze the data and understand where they can improve their operations. From checking idle times for tractors in the field, the real-time status of all equipment, to what product is being applied and at what rate, all with push notifications from the Operations Center that inform managers of current issues.
The data provided can also help customers predict when a specific job will be completed, and how much battery life is left, allowing them to prepare for tasks such as re-charges, and get them to the next task more efficiently and quickly. Data-driven decision making for customers is John Deere’s goal with the Operations Center.
While all tractors currently can be retrofitted with a 4G modem, if it isn’t already installed, rural customers who may struggle with internet capabilities now also have the option of installing JD Link Boost, in partnership with Starlink, which is their satellite connectivity product. This will help customers utilize electronic and E-powered equipment consistently and assuredly.
With BEV machines, charging stations are a crucial detail. According to Deere, there will be different options that take into consideration the infrastructure that each customer has on their operation. Their approach to assessing each area that will need a charging station can be done using virtual technology (think Google Maps) and meeting with each customer to define their individual needs. The service would include site assessment, project management, constructions, and commissioning of the chargers.
Customers are given the freedom to choose which electrical contractors they’d like to work with, if it isn’t John Deere, but the goal is that customers can leverage the infrastructure already in their shop or on their operations at a low cost to properly build charging stations.
Charging capacity plans are to include level two (AC) and level three (DC) chargers. The higher in capacity customers go, the quicker charging time is. The different chargers are a 350 kilowatt DC, 100 kilowatt DC, and a 16.9 kilowatt. These chargers will have charge management software to schedule charging.
John Deere said it is evaluating third-party companies to create the ideal charging station setup to fit customer needs, from cord length, electrical contractors, location of charging station on property, to supplemental charging for when tractors need a “jump start.” The representatives emphasized that their goal to make this lineup of tractors powerful enough to not need any additional charging throughout the work day besides that lunch-hour re-charge.
John Deere is testing out a few different charging packages at the enterprise level with their dealers and then will roll out to customers. Charging decisions will consider how much storage vehicles have, what each operation demands and how quickly the machines will need to be re-charged and put back into work, as well as what pricing level customers would like to stay at.
The company unveiled its new autonomous technology during CES 2025, which showcased a second-generation autonomy kit that combines advanced computer vision, AI, and cameras to help the machines navigate their environments.
According to a news release, “Select machines will be autonomy ready from the factory and the second-generation perception system will be available as a retrofit kit for certain existing machines, providing customers with multiple paths to adoption based on where they are in their technology journey.
The machines are managed via John Deere Operations Center Mobile, the company’s cloud-based platform. By swiping left to right to start, the machine can be started once placed in the appropriate spot. Through the app, users also have access to live video, images, data and metrics, and the ability to adjust various factors like speed. In the event of any job quality anomalies or machine health issues, users will be notified remotely so they can make necessary adjustments.”
Each machine in the BEV lineup is embedded with these autonomy capabilities from the start, that allow for the same technology and hardware seen on their diesel tractors, with “pods” and cameras mounted in different areas of the machine, and will be compatible with the John Deere Operations Center.
Markie Hageman Jones majored in agribusiness at Fort Hays State University. She is actively involved in her state Cattlemen’s Association, Young Farmers chapter, and National Cattlemen’s Beef Association. Her AGDAILY.com articles can be found here.